When should your forklift battery be recharged?
Forklift batteries are the lifeblood of electric material handling operations. Their proper maintenance, particularly recharging, is crucial for maximizing productivity, minimizing downtime, and ensuring the longevity of these expensive assets. However, determining the optimal time for recharging isn't always straightforward. It involves understanding battery characteristics, operational demands, and best practices. This article delves into the intricacies of forklift battery recharging, providing a comprehensive guide for operators and maintenance professionals.
Understanding Forklift Battery Basics
Most electric forklifts utilize lead-acid batteries, known for their robust performance and cost-effectiveness. These batteries operate through electrochemical reactions, storing and releasing energy. During discharge, sulfuric acid reacts with lead plates, producing lead sulfate and releasing electrons to power the forklift. Recharging reverses this process, converting lead sulfate back to lead and sulfuric acid.
Key parameters to consider include:
State of Charge (SOC): The percentage of remaining battery capacity.
Depth of Discharge (DOD): The percentage of battery capacity that has been used.
Voltage: An indicator of the battery's SOC, though not a perfect measure.
Temperature: Affects battery performance and charging efficiency.
Electrolyte Level: Must be maintained for proper battery function.

The 80% Rule and its Variations
A common guideline is the "80% rule," which suggests recharging the battery when it reaches 20% SOC (80% DOD). This rule aims to prevent excessive discharge, which can lead to sulfation—the formation of lead sulfate crystals that reduce battery capacity and lifespan.
However, the 80% rule isn't universally applicable. Factors that necessitate adjustments include:
Operational Intensity: High-demand environments with continuous operation may require more frequent recharging, potentially even before reaching 20% SOC.
Ambient Temperature: Extreme temperatures can accelerate discharge and impact charging efficiency. In hot environments, more frequent charging might be necessary. In cold environments, battery performance decreases, and charging times may increase.
Battery Age and Condition: Older batteries or those with signs of sulfation may require more frequent recharging to maintain performance.
Specific Battery Type: Some advanced lead-acid batteries or lithium-ion batteries have different optimal discharge and recharge characteristics.
Visual Indicators and Monitoring Tools
Operators can use visual cues and monitoring tools to determine when to recharge:
Battery Discharge Indicators (BDI): Many forklifts are equipped with BDIs that display the battery's SOC. Some BDIs provide visual warnings when the battery is nearing a critical level.
Voltage Monitoring: While voltage readings can provide a general indication of SOC, they are not always accurate, especially under load.
Amp-Hour Meters: These meters track the amount of energy discharged from the battery, providing a more precise indication of SOC.
Battery Monitoring Systems (BMS): Advanced BMS systems provide real-time data on battery voltage, current, temperature, and SOC, enabling proactive maintenance and optimized charging.
Charging Practices and Best Practices
Proper charging practices are essential for maximizing battery lifespan and performance:
Opportunity Charging: Partial charging during breaks or idle periods can help maintain battery SOC and reduce the need for full discharges. However, frequent, shallow opportunity charging can lead to thermal rise and electrolyte stratification if not done correctly.
Equalization Charging: A controlled overcharge performed periodically to balance individual cell voltages and remove sulfation. Typically performed weekly or bi-weekly.
Proper Charger Selection: Using a charger that matches the battery's voltage and capacity is crucial. Incorrect chargers can damage the battery.
Temperature Compensation: Many modern chargers offer temperature compensation, adjusting charging parameters based on ambient temperature.
Electrolyte Maintenance: Regularly checking and maintaining electrolyte levels is essential. Distilled water should be used to replenish lost electrolyte.
Cooling and Ventilation: Batteries generate heat during charging, so adequate cooling and ventilation are necessary to prevent overheating.
Record Keeping: Maintaining detailed records of battery charging, maintenance, and performance can help identify trends and optimize battery management.
Lithium-Ion Considerations: Lithium-ion batteries have different charging requirements. They do not suffer from sulfation, and they can be opportunity charged much more effectively than lead acid, without the risks. They have internal BMS systems that protect them, and provide data.
The Dangers of Deep Discharge
Consistently deep discharging forklift batteries (below 20% SOC) can have severe consequences:
Sulfation: The buildup of lead sulfate crystals, reducing battery capacity and lifespan.
Plate Damage: Deep discharge can cause physical damage to the battery plates, leading to premature failure.
Reduced Run Time: As battery capacity decreases, forklifts will require more frequent recharging.
Increased Maintenance Costs: Damaged batteries require more frequent repairs or replacements.
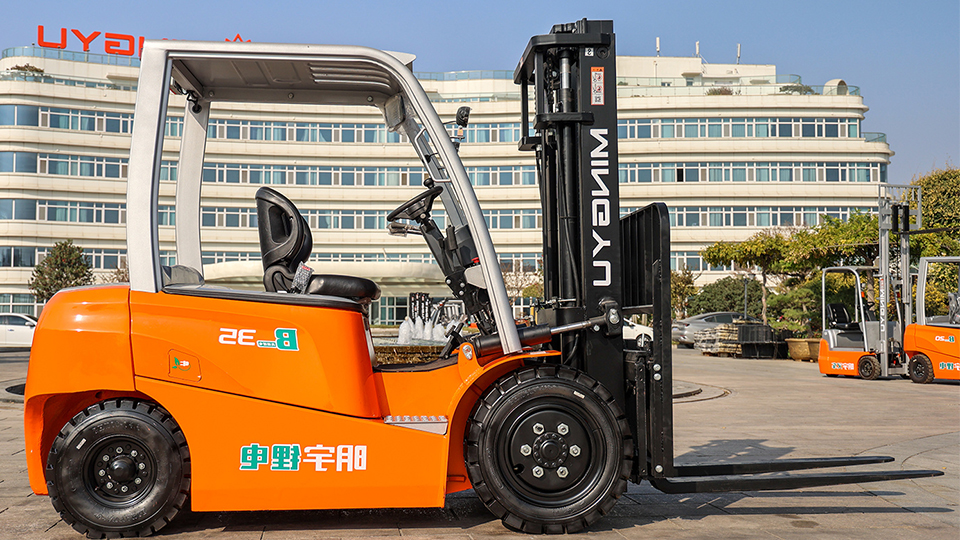
Optimizing Battery Life
To optimize forklift battery life and performance, consider these strategies:
Operator Training: Educate operators on proper battery handling and charging procedures.
Regular Maintenance: Implement a preventive maintenance schedule, including electrolyte checks, cleaning, and inspections.
Load Management: Distribute loads evenly to reduce stress on the forklift and battery.
Facility Layout: Optimize facility layout to minimize travel distances and reduce battery strain.
Battery Rotation: In multi-shift operations, rotate batteries to allow for proper cooling and charging.
Invest in new technologies: Lithium ion batterys are becoming more and more common place, they are a large upfront investment, but pay off through less down time, and longer usage life.
Consult Experts: If you are unsure about you specific needs, Consult with battery and forklift specialists.
In conclusion, understanding the factors that influence forklift battery discharge and implementing proper charging practices are essential for maximizing battery lifespan and operational efficiency. By adhering to the guidelines outlined in this article, operators and maintenance professionals can ensure that their forklift batteries provide reliable performance for years to come.